Single-Head Double-Position Vertical Winding Machine
Product Characteristics
● Single-head double-position vertical winding machine: when one position is working, another one is waiting; has stable performance, atmospheric appearance, fully open design concept and easy debugging; widely used in various domestic motor production enterprises.
● Normal operating speed is 2000-2500 cycles per minute (depending on stator thickness, coil turns and line diameter), and the machine has no obvious vibration and noise.
● The machine can arrange coils neatly in the hanging cup, especially for stator winding with high output requirements, automatic winding, automatic jumping, automatic processing of bridge line, automatic cutting and automatic indexing are completed in sequence at one time.
● The man-machine’s interface can set the parameters of circle number, winding speed, sinking die height, sinking die speed, winding direction, cupping angle, etc. The winding tension can be adjusted, and the length can be adjusted arbitrarily by the full servo control of the bridge line. It has the functions of continuous winding and discontinuous winding, and can meet the requirements of 2 poles, 4 poles , 6 poles and 8-pole motor coil winding.
● Saving in manpower and copper wire (enameled wire).
● The machine is controlled by precise cam divider. The rotary diameter is small, the structure is light, the displacement is fast, and the positioning is accurate.
● With the configuration of 10 inch screen, more convenient operation; support MES network data acquisition system.
● Its merits are low energy consumption, high efficiency, low noise, long working life and easy maintenance.
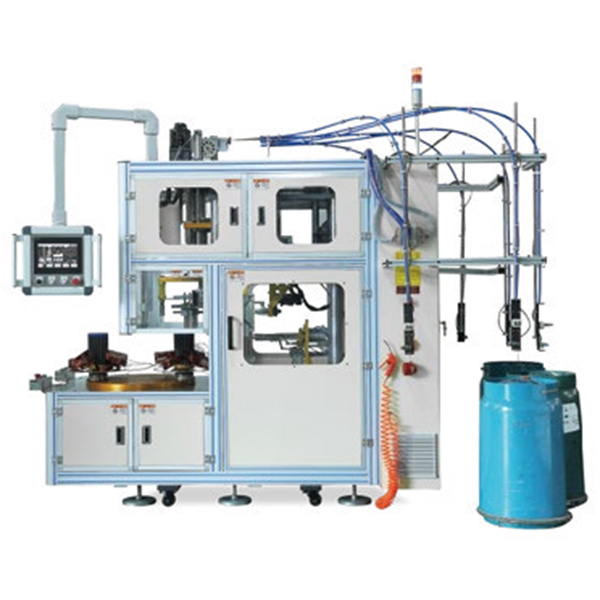
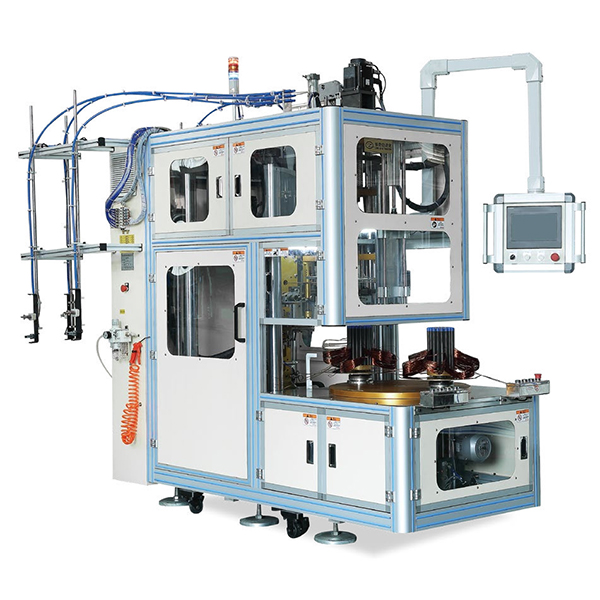
Product Parameter
Product number | LRX1/2-100 |
Flying fork diameter | 180-450mm |
Number of working heads | 1PCS |
Operating station | 2 stations |
Adapt to the wire diameter | 0.17-1.5mm |
Magnet wire material | Copper wire/aluminum wire/copper clad aluminum wire |
Bridge line processing time | 4S |
Turntable conversion time | 2S |
Applicable motor pole number | 2、4、6、8 |
Adapt to the stator stack thickness | 15mm-300mm |
Maximum stator inner diameter | 200mm |
Maximum speed | 2000-2500 circles/minute |
Air pressure | 0.6-0.8MPA |
Power supply | 380V three-phase four-wire system 50/60Hz |
Power | 8kW |
Weight | 1.5T |
Dimensions | (L) 2400* (W) 900* (H) 2100mm |
FAQ
Issue : Conveyor Belt Not Working
solution:
Cause 1. Make sure the conveyor belt switch on the display is turned on.
Reason 2. Check the parameter setting of the display screen. If the setting is incorrect, adjust the conveyor belt time to 0.5-1 second.
Reason 3. If the governor is closed and cannot work normally, check and adjust to a suitable speed.
Issue: The diaphragm clamp may detect a signal even though the diaphragm is not connected.
Solution:
This can happen for two reasons. First, the negative pressure value of the test meter may be set too low, causing no signal to be detected even without the diaphragm. Adjusting the setting value to an appropriate range can solve the problem. Second, if the air to the diaphragm holder is obstructed, it may cause the signal to continue to be detected. In this case, cleaning the diaphragm clamp can do the trick.
Issue: Difficulty attaching the diaphragm to the clamp due to lack of vacuum suction.
Solution:
This problem can be caused by two possible reasons. First of all, the negative pressure value on the vacuum gauge may be set too low, so that the diaphragm cannot be sucked normally and the signal cannot be detected. To solve this problem, adjust the setting value to a reasonable range. Secondly, it may be that the vacuum detection meter is damaged, resulting in a constant signal output. In this case, check the meter for clogging or damage and clean or replace if necessary.