Electric motors are an essential part of modern industry, powering a multitude of machines and processes. They are used in everything from manufacturing to transportation, healthcare to entertainment. However, selecting the right electric motor can be a daunting task for a business as there are many factors to consider. In this quick guide, we'll outline some basic elements to consider when selecting an electric motor for an industrial application.
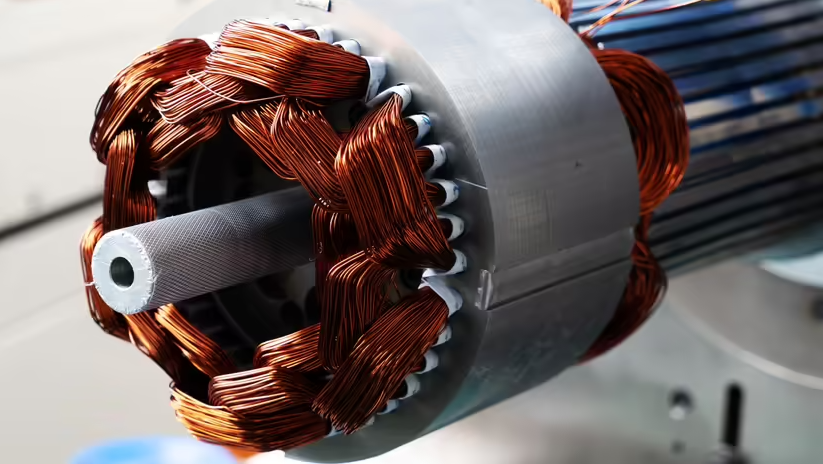
1. Torque and speed requirements:
The first considerations when selecting a motor are the torque and speed requirements of your application. Torque is the rotational force produced by the motor, while speed is the rotational speed. You need to choose a motor that can provide enough torque and speed for your operation. Some applications require high torque but low speed, while others require high speed and low torque.
2. Power supply:
Motors need power and you need to make sure the electrical rating of the motor is compatible with your power supply. Most electric motors require either AC or DC voltage and you will need to select a motor that matches the power available. The voltage and frequency of the power supply should also match the requirements of the motor.
3. Shell type:
Electric motors are available in a variety of enclosure types that provide varying levels of protection against environmental factors such as dust, moisture, and temperature. Considering the environment in which the motor will operate, you must select the proper enclosure type for your application. Some common motor enclosures include TEFC (Totally Enclosed Fan Cooled), ODP (Open Drip Proof), and Explosion Proof.
4. Efficiency and energy consumption:
Efficiency is an important factor to consider when selecting a motor. A more efficient motor consumes less energy to produce the same power, reducing operating costs and increasing energy efficiency. Look for motors with high efficiency classes such as IE3, IE4 and NEMA Premium. These motors also generate less heat, reducing the need for cooling systems.
5. Maintenance requirements:
Electric motors require maintenance throughout their life cycle, and you need to consider the amount of maintenance required when choosing a motor. Low maintenance motors are ideal for applications where regular maintenance is challenging, such as remote locations. When choosing a motor, you should also consider spare parts availability and repair costs.
6. Motor size:
The size of the motor is another key factor to consider when selecting a motor. The motor size should match the load requirements to prevent overloading or underloading. Choosing a motor that is too small for an application can result in loss of efficiency, while choosing a motor that is too large can lead to overruns and inefficiencies.
7. Noise and vibration:
Noise and vibration levels are fundamental factors to consider when selecting an electric motor, mainly where noise level is an important issue. Some motor designs generate more noise and vibration than others, and you will need to select a motor that is compatible with the noise level of your environment.
8. Motor life:
The life expectancy of the motor is another important factor to consider. Longer-lasting motors generally provide better value because they require less frequent replacement, reducing downtime and maintenance costs. You should consider the quality, durability and reliability of the motor to determine the expected service life.
In summary, selecting the right motor for your industrial application can be complex, with multiple factors to consider. The most critical factors to consider include torque and speed requirements, power supply, enclosure type, efficiency and energy consumption, maintenance requirements, motor size, noise and vibration, and motor life. Careful consideration of these factors, and working with an expert in the field, will ensure you select the correct motor for your application, resulting in increased efficiency and lower operating costs.
Post time: Apr-26-2023